Case Study: How a 3D-Printed Tool Saved Thousands of Hours and Dollars
THE CHALLENGE
Due to the COVID-19 pandemic, a vendor of Würth Des Moines Bolt (DMB) that assembled a sealing plug stopped their assembly service. To continue to meet customer demand, DMB’s kitting department began building the plugs in house.
To assemble the plug, an O-ring needs to be stretched over the threads to sit below the head of the plug. During assembly, the threads scratched employee’s hands, slowing down production and limiting the number of plugs that could be assembled in a day. Due to the slow pace, building the plugs began to take up more and more time and DMB risked falling behind customer demand.
DMB’s Kitting Manager came to Angela Curtiss, a Process & Quality Engineer located in Des Moines, to create a solution in the form of a 3D-printed assembly tool to install the O-rings onto the plugs.
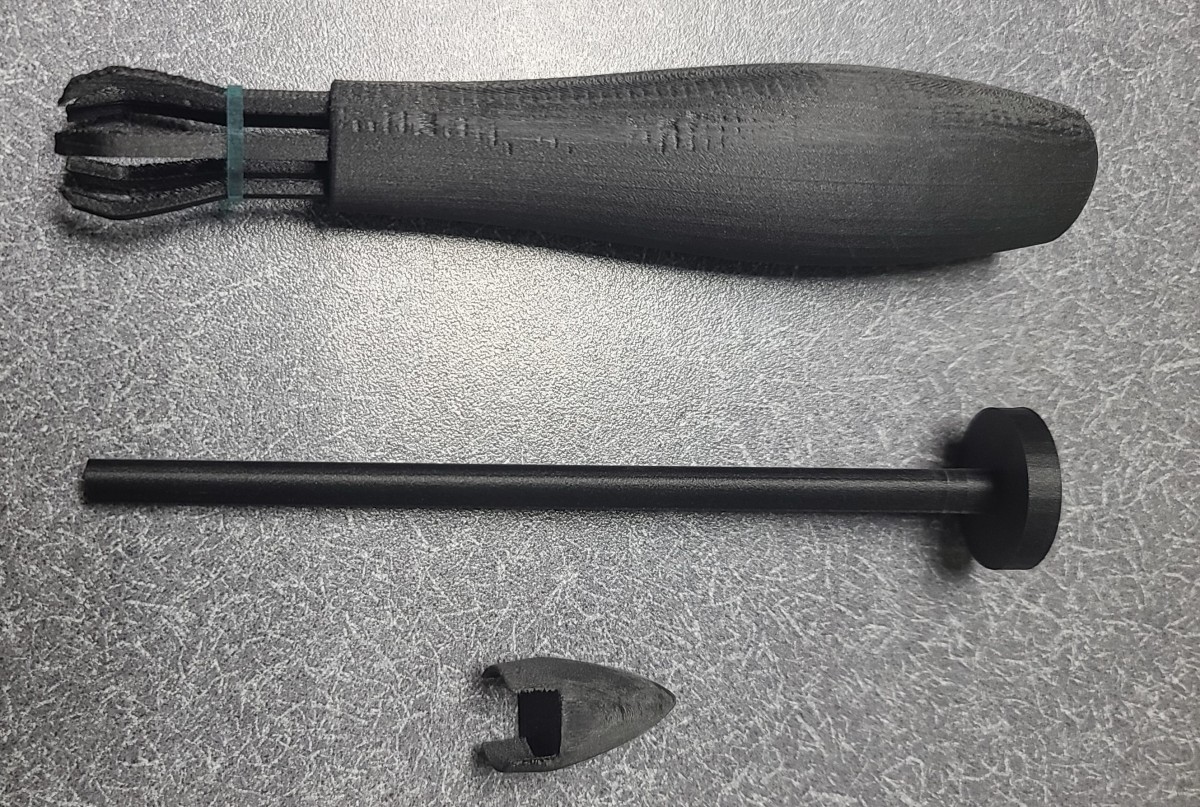
THE SOLUTION
The tool consists of a cap, a handle, and an ejector pin. The handle was printed with extra thick walls and secured with a rubber band to prevent deflection in the teeth during use. The handle pushes the O-ring over the cap until it is seated below the head of the plug. Then, the ejector pin pushes the cap out of the teeth of the handle.
Development took about 1-2 weeks' time. Angela created eight total iterations of different parts of the tool, printing and testing each part combination at the facility with the product assembly.
When assembling the plugs by hand, a single employee could complete 100 plugs per shift, but would be unable to assemble any in the following shift due to hand fatigue. Now, a single employee can assemble 3000 plugs per day on consecutive days. DMB is now able to keep up with the 6500 monthly customer demand with just over two days of labor. Each set costs $10.04 and takes 11 hours to print and has saved DMB's customer over $92,800 since its implementation.
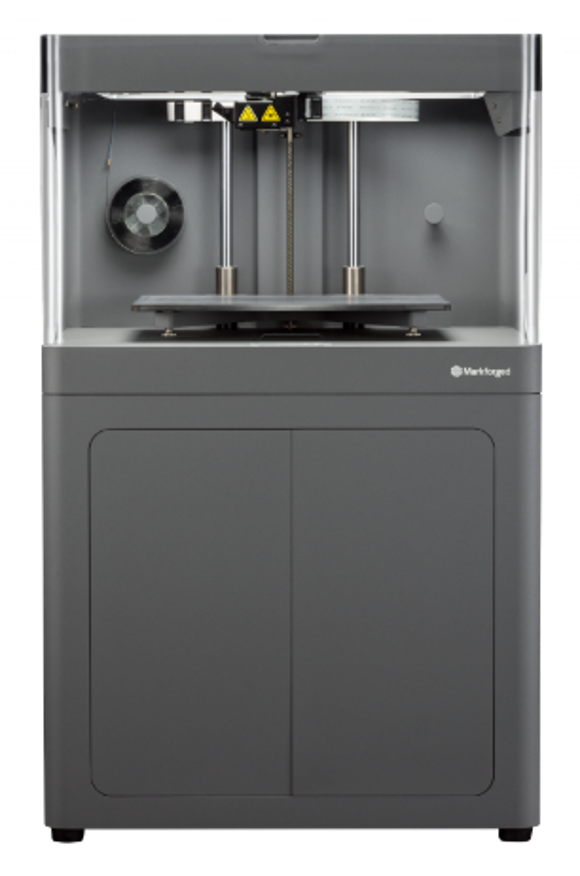
The assembly tool was printed on the Markforged X7. The X7 is Markforged’s highest-end industrial model, capable of printing with every type of Markforged’s printing material.
The install tool was printed with Onyx, a proprietary material combination of 6/6 Standard Nylon and chopped-up carbon fibers, which every Markforged printer at every price point can print with. Onyx creates a stronger base than nylon alone. Depending on the model of printer, additional carbon fiber, or other fibers can be added to the material.
This project truly illustrates the power of additive manufacturing, not only for printing parts or part prototypes, but also for creating tools, and other fully customizable solutions to production problems.
In addition, much of this process was completed remotely—Angela was able to work on the tool designs and send them to the printer right from her home office.
With a Markforged printer and support from our 3D Team, you have a powerful resource for streamlining your production at your fingertips.
Learn more about how you can implement additive manufacturing in your application. Get Started!
Click here to shop printers, filaments, and other consumables in Würth Additive Group's online store.
Follow Würth Additive Group on Instagram!
View Terms and Conditions for Würth Additive Group's Instagram giveaway.
Follow Würth Additive Group on Instagram!
View Terms and Conditions for Würth Additive Group's Instagram giveaway.