The 4 Key Elements of Additive Manufacturing
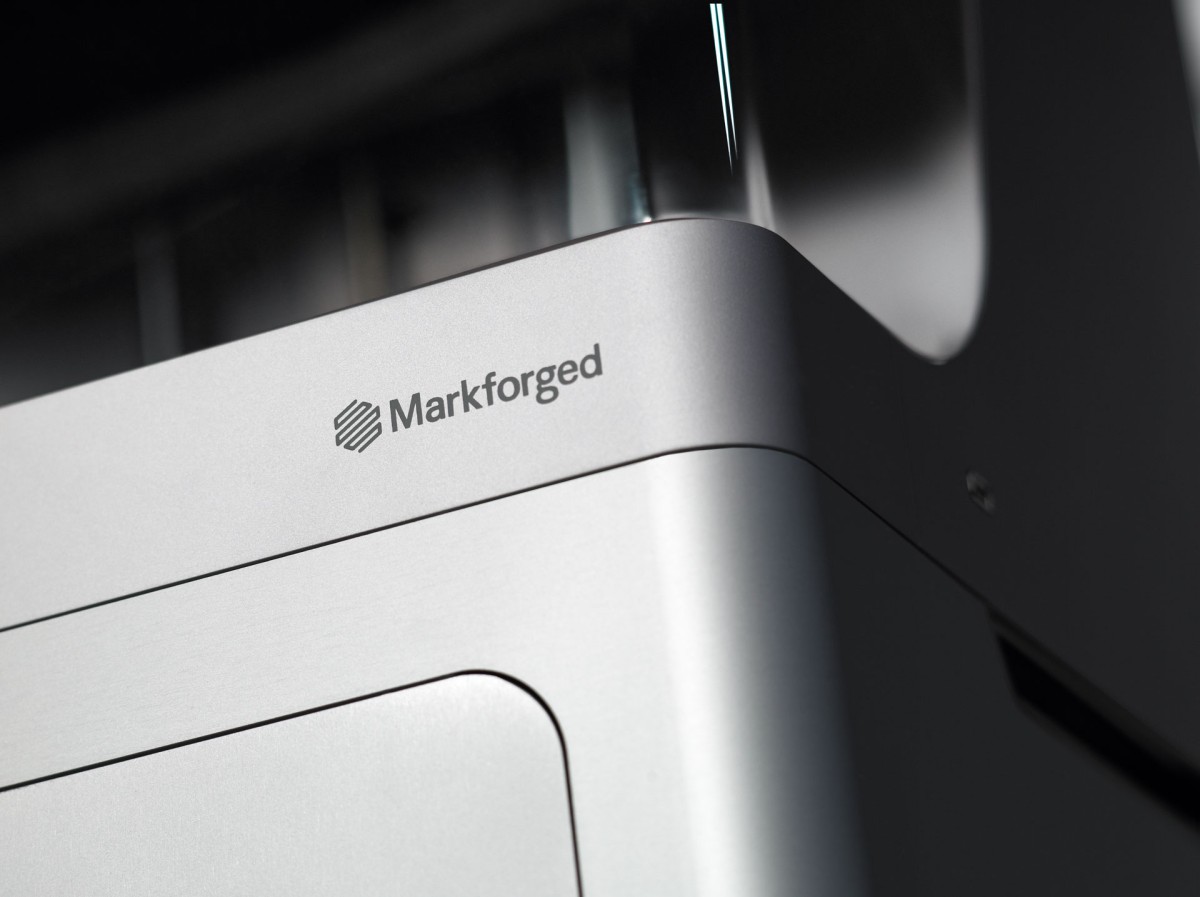
While industry experts hypothesize the benefits of additive manufacturing, Markforged and Würth customers are already leveraging industrial 3D printing on every continent and delivering ROI in every stage of the development cycle. Here are the four key ways they’re using 3D printing to improve their supply chains, factories, and products:
1. Peak Performance Through Unparalleled Design Freedom
Additive brings a new set of capabilities to the concept of "Design for Manufacturing." While traditional manufacturing is limited by cutting processes, geometry, and tool access, additive allows engineers and designers to access complex geometries and infills never thought possible.
2. Engineering-Grade Durability with High-Strength Parts
Advancements in additive materials with high-strength properties open up an entirely new and more productive range of manufacturing applications. Markforged Onyx reinforced with continuous carbon fiber produces parts that have strength comparable to machined aluminum, but at a fraction of the weight. 3D printed metals allow for all the benefits of traditional steels and alloys, along with a newfound flexibility and accessibility.
3. Accurate, Reliable, and Repeatable Parts
The speed and repeatability of 3D printing allows users to rapidly and reliably iterate from prototype to final part. 3D printing empowers manufacturers to move faster than their competitors, whether it’s to replace a part, create a proof of concept, or retool their factory line.
4. Print from the Cloud — Anywhere in the World
Additive cloud solutions empower on-demand part production through a digital inventory, reducing reliance on traditional inventory and supply chain costs. Users of 3D printing can restructure their business models to create parts whenever and wherever needed. With all of these advantages available today, the question now is “what’s next?”
Looking to Tomorrow
Additive manufacturing is taking businesses to a completely new level of efficiency in manufacturing. Expensive physical storage is changing to digital inventories with on-demand parts. Manufacturing lines are being adapted on-the-fly with flexible, on-site tool production. Engineers are developing new products faster with better performance and optimized geometries.
The innate flexibility of 3D printing makes it easier for companies to adapt and accommodate new customer and industry demands. It lets manufacturers quickly respond to unpredictable environments, regulations, or shifts in the market. The agile tool allows engineers to respond creatively to any situation — whether there’s a supply chain shock from a pandemic or demand spike from a new trend in consumer preferences.
The ease, versatility, and design freedom of 3D printing are here now. On the horizon is a world of full-scale adoption, optimized supply chains, and parts sold from digital inventories, but the stories outlined in this report mark the success of just how far 3D printing technology has come and serve as a precursor for what’s next.